Savage Arms is located in what was long known as New England’s Gun Valley, where George Washington placed Springfield Armory in 1777, to store muskets, cannons and where cartridges and gun carriages for the American Revolution were made.
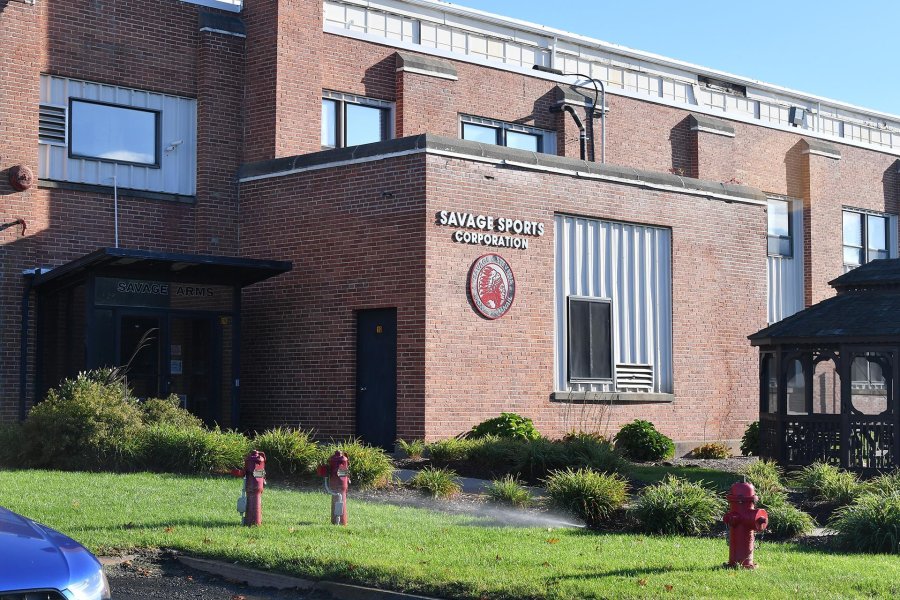
The Connecticut River Valley then became birthplace to most of America’s early gun manufacturers, the likes of Colt, Remington and Smith & Wesson. While Savage Arms was founded by Arthur Savage in Utica, NY in 1894, the company purchased Stevens Arms in Massachusetts in the early 1920s, gaining a foothold in the Springfield area. Along building and selling its own sporting firearms, Savage has been pivotal for American war efforts in both World War I and WWII, and finally relocated in the 1960s to Westfield, a few miles west of Springfield, where it still is today.
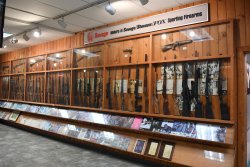
And today Savage is a force to be reckoned with – the decades from the 1960s passed with their highs and lows, and few years have passed since 2019, when the company was purchased back from Vista, and under which the company had the chance to restructure, growing to be one of the leaders in the US and the world’s sporting and hunting firearms market.
To complement the wealth of innovations that the manufacturer is famous for, such as the Barrel Locknut, the Accutrigger, Accufit and Accustock, and more, Savage has introduced many new products including the first ever American engineered and built a straight-pull bolt action rifle, with an interesting seldom-seen locking system, similar to the Heym ball locking system of the SR30, that Savage called Hexlock: the Impulse (here is our article). And why this specific product is central to this story, will be clear in a minute.
Savage: building you own personal hunting rifle
all4shooters.com has been selected by Jens Tigges from Outdoor Marketing International, a German firm representing Savage in Europe, to perform a factory tour at Savage Arms, in an unforgettable journey that also included a once in a lifetime Pronghorn hunt in Colorado – and part of this experience is hand-building our own, personal hunting rifle right off the same assembly benches where the Savage bolt action rifles are built. Obviously, the rifle I have built at Savage is a custom name-engraved version of the Impulse Mountain Hunter, in the powerful and brand-new 7mm PRC caliber. But, lets go on.
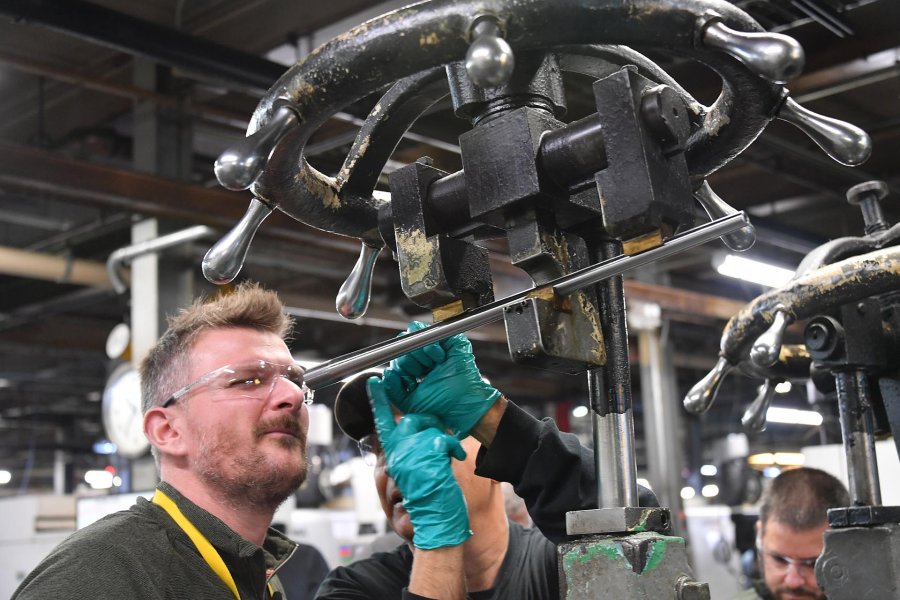
My first impact with the Savage Arms factory is with the exterior of the building; rather unremarkable, very much like many other red-brick Government and production buildings of post-war New England. Inside, a museum-like entrance shows off all the Savage firearms and products except one: the .45 ACP caliber semiautomatic entry to the 1906 Army Trials which was lost to the Colt 1911, and that gave birth to the Savage 1907 in .32 and .380 ACP. Only 181 guns of the .45 ACP model were ever built, and very few of these are known to exist in private hands.
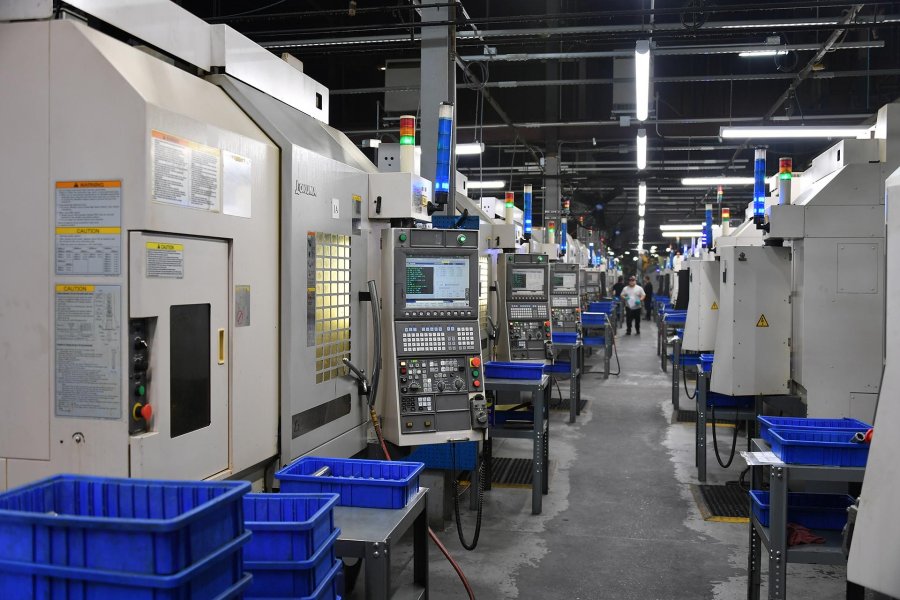
After a brief meeting with the management, our tour starts immediately; the atmosphere is very relaxed and I marvel at how at-ease all the employees, machinists, assemblers, and specialized workers all seem to be. I realize that there must be multiple generations of workers simultaneously at their workstations: it would not surprise me if there were fathers and sons (or daughters, for that matter!) working alongside each other. Our guide, Wayne Kratochvil, the senior materials supervisor, has been with the company an astounding 39 years!

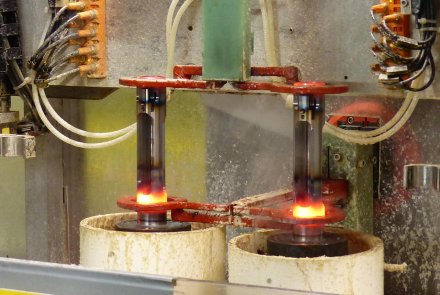
The same happens with the receivers: due to time constraints, our tour explored only the bolt action manufacturing line, but we did get to see the occasional pistol frame or slide being worked on. The 110 action based models all have the receivers made of steel, and we followed the bar stock since drilling, reaming for the locking lugs, multiple axis machining and threading, induction hardening and then surface treatment; while the Impulse straight-pull bolt action receiver is made of 7075-T6 alloy, since the barrel of this gun features a barrel extension in which the bolt locks in, not dissimilar in functionality to the AR, therefore the receiver bears no pressure.
It is refreshing to see how much skill is needed to build a barrel. Not only the button rifling is manually done, with a seemingly simple and fast operation, but the contoured barrels blanks, each and every one of them, are hand straightened just before chamber reaming using a completely manual fixture, by a superbly skilled and experienced operator.

It is also obvious that the 600 or so employees that make up the company’s workforce, and their skill set, is very valued in Savage, and they are actually referred to as “Team Savage” by Mr. Kratochvil many times in our visit.
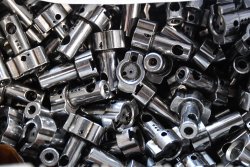
All parts lots also need to be checked in the quality control facilities, where samples are routinely tested.
While all this is happening, in the assembly lines and on various cell benches assemblers put together individual parts into subassemblies such as completed bolts and trigger packs, testing them and preparing them.
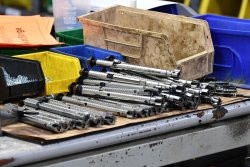
Of course, it all converges on the final assembly shop, where the firearms are completed by putting together the various subassemblies. It is interesting to note that the final assembly lines are organized so that many small batches of rifle models can be simultaneously built to order, rather than having scheduled, rigid, and dedicated production runs of individual models built in thousands of copies. This allows Savage to build and deliver exactly what is needed in a matter of days to the customer, and also avoids having excessive quantities of stocked products in storage.
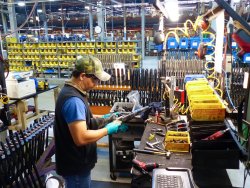
This is also where I have been invited to assemble my rifle, already prepared on a working trolley with all relevant parts and… my name nicely engraved on the receiver! The completed guns are all test-shot in the indoor range. But enough words: as they say, an image is worth a thousand words – and a video, double that.
To wrap up, my visit at Savage has been an amazing experience, and building the impulse rifle doubly so! Handling that gun on the range at during the Pronghorn hunt always reminded me of the people at Savage that built it, and I’m honored to have at least been a very, very small part of that process in completing my gun.
Stay tuned for a complete test of the Savage Impulse Mountain Hunter straight-pull, bolt action rifle in the hot 7mm PRC caliber, soon on all4hunters!
For more information: www.savagearms.com.