When the topic comes to Thermal Imaging Optics, one of the most debated subjects is NETD, both because it’s often misunderstood, and because of the way it is marketed by the manufacturing companies and how it is measured. Suffice to say, NETD value has become a primary parameter to compare different thermal imaging cameras.
Pulsar therefore officially introduces the concept of “system NETD”. Until today, Pulsar used to share the NETD of the sensor used. Other brands often lean towards sharing system NETD of their thermal imaging optics. Now, Pulsar has decided to do both.
NETD, a misunderstood metric
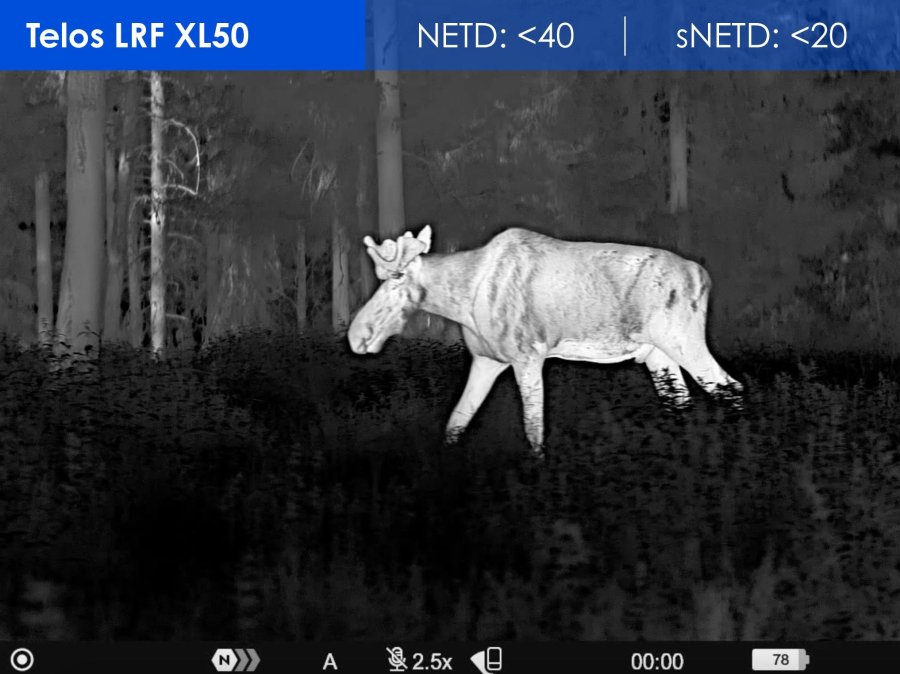
What does NETD stand for? It means “Noise Equivalent Temperature Difference” and it is essentially a metric that describes the sensitivity of the FPA sensor inside a Thermal Imaging camera: more specifically, it is the smallest detectable temperature difference between an object and its background. It is expressed in Kelvin degrees, and a smaller number means more sensitivity, therefore better performance.
While in dry, clear weather conditions with high thermal contrast the difference between a 40 mK and 25 mK NETD camera may be subtle and not immediately apparent, as in this case the big improvement is made by the number of elements, or pixels, composing the sensor – hence a higher native FPA resolution yields better images – NETD becomes very important when observing a low thermal contrast environment, in which most objects have very similar temperatures, such as during rain and fog.
A low NETD allows a thermal imaging camera to discern between different objects, identify them and distinguish subtle details. A practical example: a thermal imaging camera with a 40mK NETD sensor can theoretically detect and distinguish a 10,04 °C leaf floating over 10 °C water. A 25mK NETD camera will allow you to see detail, such as the leaf’s midrib and even the veins in the same conditions.
Worth mentioning: the value of 1 Kelvin is the same of 1 degree Celsius, but while 0 °C is set to freezing water, 0 K is set relative to total absence of thermal energy – so no negative K values are possible, and this is why it’s used to measure NETD.
European and American Sensor manufacturers, as an industry standard, usually test their sensors at 25 °C background temperature, normalized for an ideal F/1.0 lens with 100% transmission, and using the integration time to achieve 50% well fill. Integration time is the amount of time it takes to capture a single thermal frame – in photographic terms, it’s the exposure time. Not all manufacturers test and rate their sensors using industry standards, though.
NETD and System NETD
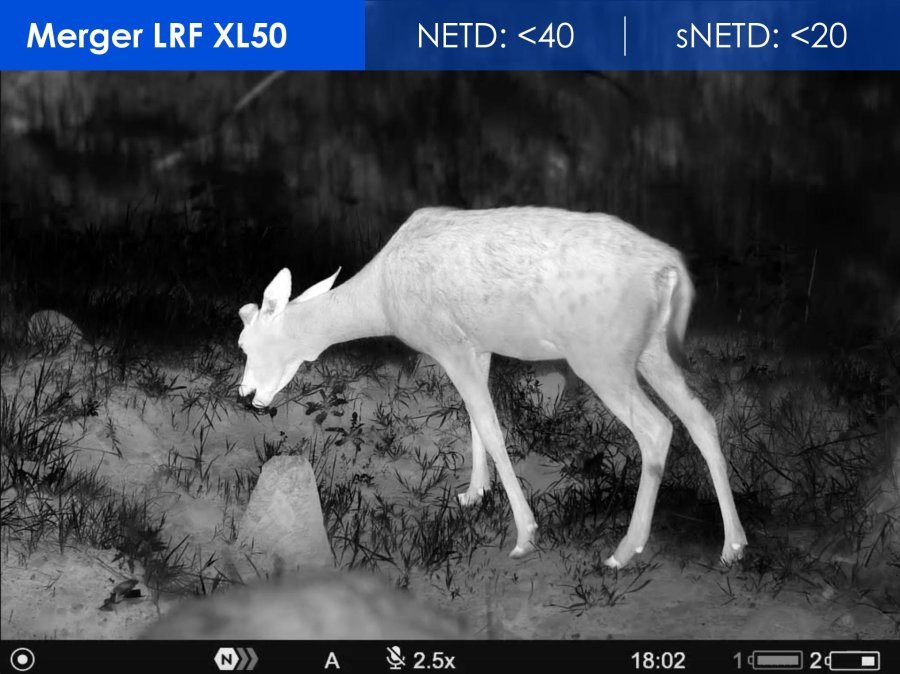
For its Thermal Imaging cameras, Pulsar has always shared the NETD figures of the sensor used, as lab tested and certified by French manufacturer Lynred, which builds Pulsar’s sensors. However, sensor NETD is a fixed, basic value that can be affected by a number of factors when integrated into a complete optical device, such as image processing algorithms and filters that are built in the optical device “system”. So, there are two types of NETD: sensor, and system. To sum it up, while base sensor NETD remains unchanged, the NETD of the system can be improved with the help of software – and this is indeed great, as long as the algorithms and software are carefully and optimally selected. It’s a fine balance; image processing parameters can reduce noise levels while also retaining useful signals and details. On the other hand, excessive processing can be used to achieve the lowest possible system NETD, while introducing artifacts, crunching fine details, and finally making the image less informative.
But there’s more: excessive use of image manipulation and processing may lead to image lag, skewed or blurred images when panning and moving the thermal camera, or observing rapidly moving objects – and as hunters or LE, this may become a serious problem if the optic we’re using is a thermal imaging riflescope.
Reading through marketing materials and ads, we see NETD values of 40, 35, 25, and 18 mK. The lower the value of NETD, the more proudly the thermal imager is advertised.
Comparing NETD
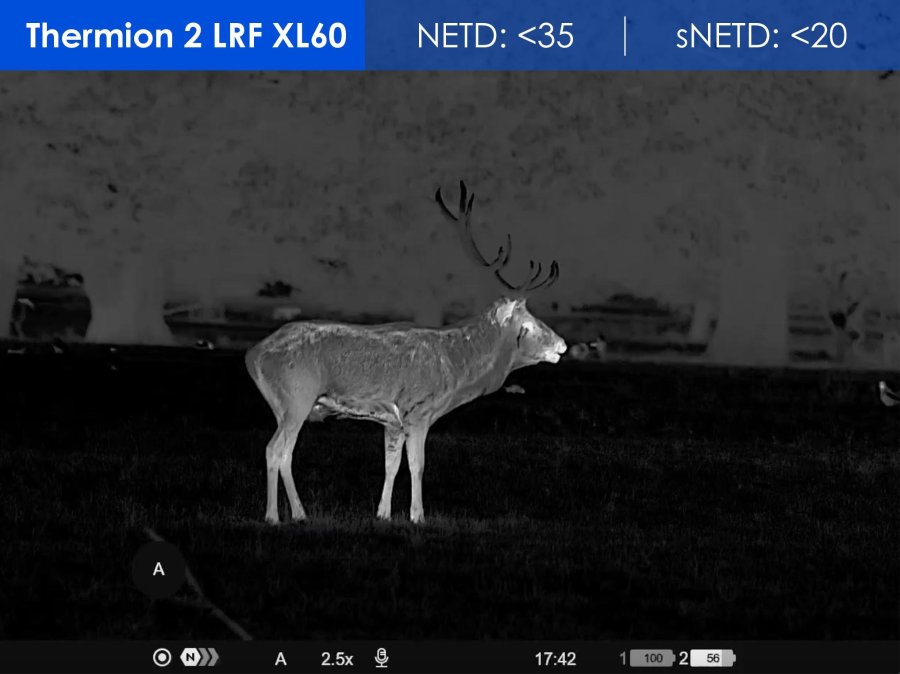
How do you compare NETD values of different optics on the market? The problem lies with the fact that while measuring sensor NETD does in fact follow sort of an industry standard, and most western countries manufacturers do adhere to it – with small differences – system NETD is not considered an industry standard, since it is achieved with software and algorithms; it is next to impossible to regulate it. So, in comparing devices, Pulsar recommends to look for sensor NETD first, and only then take the system NETD into account.
NETD in Pulsar devices
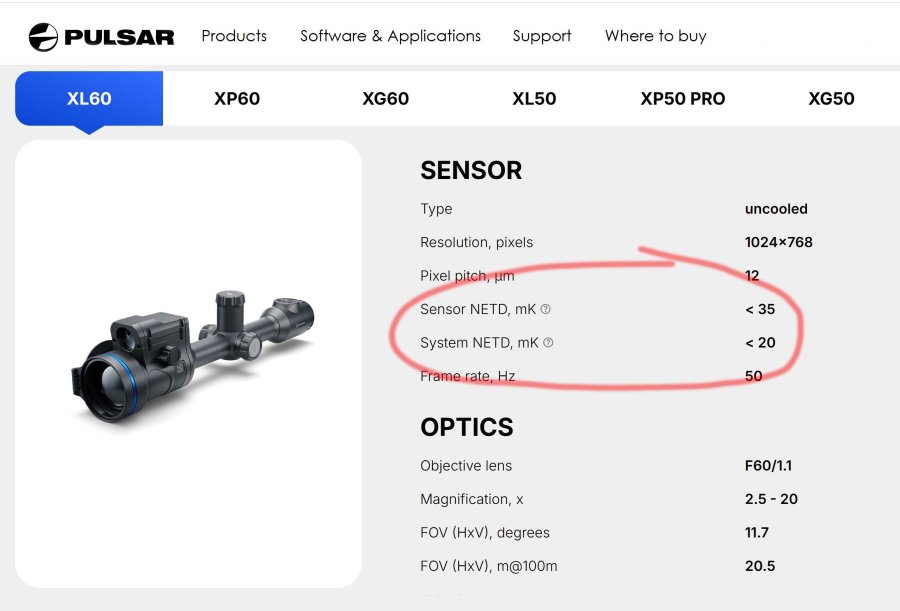
So back to the start: until recently, Pulsar didn’t share system NETD – as the European manufacturer believes that System NETD is more objective. But from now on, when you look at the specs sheet of a Pulsar device, you’ll see two numbers: NETD and sNETD. The first will always be the sensor base NETD, the number the sensor manufacturer provides. The second one – System NETD – will be calculated after all the processing algorithms come into play.
The main reason Pulsar decided to introduce the sNETD figure-of-merit is to make the prospective buyer’s life slightly easier. With many manufacturers hiding their sensor NETD, it is hard for users to accurately compare specs of thermal imaging devices. With sNETD available on Pulsar devices, you’ll be able to compare them to others more easily, while also having the true NETD value in mind.
Last but not least… NETD on paper and NETD in the field
Just like the listed maximum speed achievable by a motorcycle, NETD is just a number printed on paper. It’s calculated in a lab in ideal conditions – not in the field. Plus, while NETD may be important for a thermal imaging optic, there’s many more features that weigh in the overall performance. Quality of the optics, types, lifetime and weigh of the batteries, build of the housing and heat dissipation, eyepiece and microdisplays used… the list goes on and on. It is always recommendable to test a thermal imaging optic in actual field conditions before purchasing if that’s possible.