The Dillon XL650 five-station press is still one of the most popular reloading machines, even though it has been out of production for several years. Ambitious shooters with high ammunition consumption often even own two of these multi-station presses, one for small and one for large primers, which eliminates the need to convert the component for primer setting. During the pandemic, the availability of Dillon products tended towards zero, there was almost nothing available from the US manufacturer. Almost everything is now available again, albeit with the bitter aftertaste that prices have increased significantly.
Dillon RL550C four-station press
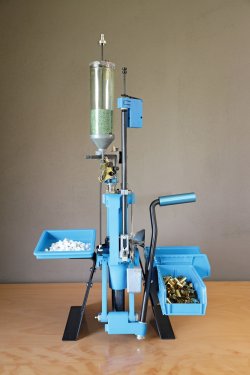
For those who like it a size smallerm this four-station press is currently available for around 720 euros without a conversion kit. For the 550, the manufacturer offers conversion kits in over 160 calibres from 7.65mm Browning to .416 Weatherby Magnum. To get started, you need such a calibre-specific conversion kit and the corresponding die set. The manufacturer promises a production rate of 400-600 cartridges per hour. That's quite a lot, because the aluminium frame press does not have an auto-index and the plate has to be turned by hand. Care is required here, if you forget to turn the disc once, you have a double powder charge in the case. For this reason, we recommend designing the loads in such a way that you select a loading density of more than 50%, so that double loads are noticed when the cases are full or overflowing. There is no room for a "powder check" control mechanism on the Dillon 550, unless you sacrifice the third station, where the bullet is seated and crimped separately on the fourth station. The bullet would then have to be seated and crimped at the same time on the fourth station, and then with a third-party die.
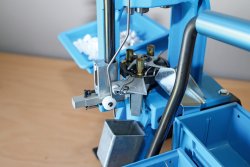
This would not be a problem, as the Dillon presses are equipped with the standard 7/8 "x14 thread. When loading, both hands must be removed from the press lever. This is because the turntable has to be turned, a bullet has to be placed on the case and a new case has to be inserted, which simply slows down the loading speed. With careful operation, 250 to 300 cartridges per hour are realistic. A case feeder would even be available as an option for the 550. The 550 is a loading press for medium consumption, which is also ideal for making rifle cartridges thanks to the manual index. The press can be converted to a different calibre very quickly in just a few simple steps. The Dillon RL550C is therefore ideal for making small quantities of cartridges in many calibres as well as precise loads for development (test loads). Over the years, the powder filler has been equipped with positive control and the coil spring, which was fitted as a return spring, has become obsolete. The lever mechanism used to be equipped with holes for dripping in oil. Today, Dillon presses are equipped with grease nipples for lubricating the mechanism. On the C model of the RL550, these are only located on the lower hinge and on the larger XL650/750 loading machines on both hinges.
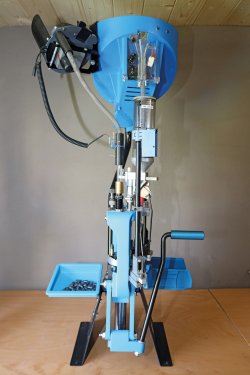
The young Dillon XL 750 multi-station press (available from strobl.cz) put to the test
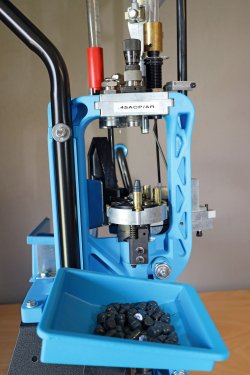
Like its predecessor, the Dillon XL 750 loading press, which was launched in 2019, is also equipped with a blue aluminium frame. In the five-station press with auto-index system, the shellplate automatically rotates one station further with each lever movement – and does so more smoothly out-of-the-box than the XL 650. Equipped with automatic case feeding, Dillon promises an hourly production rate of 500 to 800 cartridges with the XL 750. The loading machine is available for 115 calibres, from 7.65mm Browning to .338 Lapua Magnum. In our experience, the Dillon XL650/750 is particularly advantageous for in-house production of handgun ammunition. The XL750 is currently available ready to load with case feed for around €1,500. You then need a die set and the appropriate conversion kit and you're ready to go. The XL750 has the primer feed system of the 550 press; some users have had problems with the 650 system, but we cannot confirm this. The only drawback here was that the automatic system always feeds a primer.
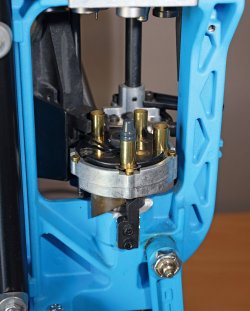
Even if the loading machine was empty or a fault occurred, for example, primers were fed that then had to be put back into the system manually. Armanov has developed the "Primer Stop Switch" for Dillon XL 650 owners, which can be used to switch the primer system on and off like a switch. We also use this tool and it is simply a "must have" for Dillon XL 650 owners. The XL 750 with the 550 system does not have this issue. This is because if you do not press the lever down to set the primer, no further primer is fed and the primer remains in the system. The XL 750 is optionally available with the new case feeder with a larger capacity and motor. The infinitely variable motor works twice as fast as the old version in the fastest setting (0 to 8 revolutions per minute). The height of the cam in the case feeder and the opening of the feed window can be adjusted from the outside. A "Powder Check" system is usually installed at station 3. This system acoustically indicates risky misloads (classic double loading or no powder in the case).
Facts, figures and specs: Dillon RL550 and XL650/750

The Dillon RL550 is a compact progressive press that is 75 cm high on the workbench without the optional case feeder (dimension to the top edge of the powder measure, the primer rod is higher when the tube is full). The Dillon 650/750 loading machines, on the other hand, reach a full height of 110 cm (top edge of case feeder tube with Dillon Strong Mount). You need a room height of at least 250 cm to work properly, including filling the case feeder tube. A calibre conversion kit for the Dillon RL550 costs around €90, while a "Quick Change Kit" for faster calibre changes costs around €210, as with the XL650/750. The large five-station presses can be quickly converted with a pre-equipped "Quick Change Kit". The author also has two machines in operation to avoid having to change the primer system. An experienced Dillon owner can manage a calibre change with the necessary cleaning of the kit components in under ten minutes. Unfortunately, a conversion kit for the 650/750 currently costs around 150 euros. In addition, a carbide die set for handgun calibres costs a hefty 165 euros. The assembly of a press is clearly explained in the English-language instruction manual in pictures and text. Before loading the Dillon XL750 with primers and cases, the dies and powder filler should be adjusted with a case using the case mouth expander.
In practice: loading with the Dillon 550, 650 and 750
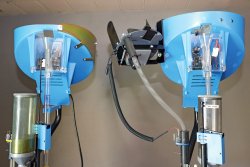
We can unreservedly recommend the Dillon 550/650/750 trio for the efficient mass production of handgun ammunition. However, the 650 can only be found on the second-hand market. Of course, it is also possible to make rifle ammunition on the presses, which we have already done, although the costs increase significantly in this case. A carbide die set from Dillon in .308 Winchester costs a hefty 360 euros.
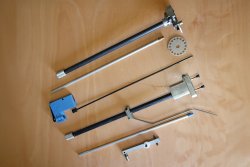
You also need an ammo checker, as you have to use it to set the depth of the die. In short, the effort and costs are considerably higher when loading rifle cartridges. The Achilles' heels of many multi-station presses are the accuracy of the powder filler and the reliability of the primer setting system. We have not had any problems with the primer system on any of the presses in many years of use. We appreciate the Dillon powder filler, it is very precise, two powder bars for medium and large loads are included in the scope of delivery. An XS powder bar, designed for extra-small loads of up to 15 grains, is available as an option. We sacrificed the "Powder Check" on the third station in good conscience thanks to the safe auto-index system and installed a "Mr Bulletfeeder" from Double Alpha Academy (DAA) instead. This allows you to easily empty a 100-bullet primer tube on the XL650/750 in five minutes if you work carefully without taking your hand off the press lever – in other words, you can produce 100 cartridges. With this set-up, picking the primer is time-consuming. Automatic primer filling systems such as the DAA Primafill, Primer Pro Collator and Prime Vibe Primer Tube Filler are worth investing.
Conclusion: what the young Dillon XL750 multi-station press can do
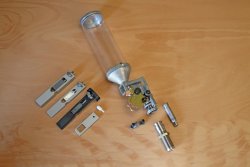
It is a tough nut to crack for the competition on the market to get past the Dillon progressive presses. With the young XL 750 and its primer slide, which only ejects primers when the loading lever is moved downwards to set a primer, Dillon has successfully managed the generation change. Last but not least, Dillon Precision from Prescott, Arizona, offers a lifetime guarantee – a fair deal all round! Dillon loaders and accessories are available from specialised dealers such as the strobl.cz webshop .
Further information on Dillon reloading products can be found on the manufacturer's website. And of course also in the strobl.cz webshop.